Chemical mechanical polishing (CMP) is an ultra-precision surface processing technology that realizes local or global flattening of the surface of the workpiece at the nanoscale through the dual coupling of chemical corrosion and mechanical grinding. In the CMP process, abrasives play a critical role as the direct effector and transmitter of mechanical and chemical effects, and their hardness, particle size, shape, dosage, and other parameters will affect the specific effect of polishing. Below, we will introduce to you in detail several types of abrasives commonly used in CMP.
Definition: What is an Abrasive, and What is a Slurry?
An abrasive is a hard material used to wear down the surface of another material through friction and grinding. In CMP, abrasives are the particles that physically remove material from the wafer surface.
A slurry is a liquid mixture that contains abrasives suspended in it along with other chemical components. In CMP, the slurry serves as both the medium that delivers the abrasives to the wafer surface and the chemical agent that aids in the polishing process.
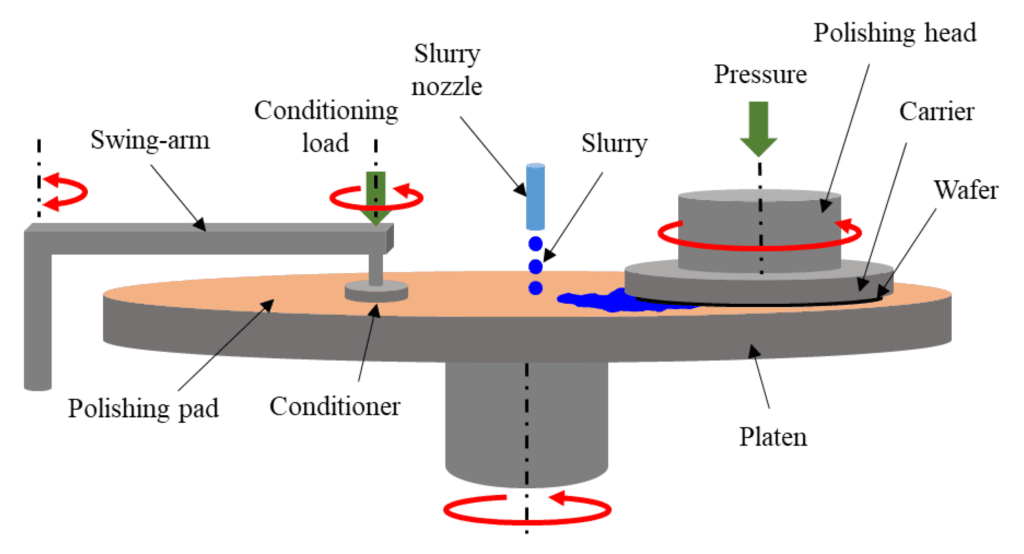
Silica sol SiO2
Silica sol is one of the most widely used abrasives in the CMP process and belongs to soft abrasives. After SiO2 is dissolved in water, it will come into contact with water to form a Si-OH bond, which makes it attached to many hydroxyl groups to form a silica sol. The silica sol is a milky white colloidal liquid. Inside, it is a three-dimensional mesh structure formed by Si-O-Si bonding, and outside, it is wrapped with negatively charged hydroxyl groups. The water molecules in the silica sol dissociate to form H3O+. Under the action of static electricity, it is adsorbed on the adsorption layer and the diffusion layer, forming a double layer.
The electronic layer structure and its thickness play a key role in the dispersion stability of silica sol in the polishing solution. The diameter of the nano-particles in the silica sol can be controlled at 10-150nm, and different particle sizes of silica sol will produce different removal rates. Through effective selection, the needs of different processes can be met; its mechanical wear performance is moderate, and the selectivity and dispersion are good, so the workpiece’s surface is affected during the polishing process. The damage is minimal, and the hardness is close to that of elemental silicon, so it is commonly used in polishing silicon, soft metals, and other materials.
Alumina Al2O3

Alumina is an abrasive with high hardness and good grinding properties. It has a variety of heterogeneous phases in nature. Among them, α-Al2O3 is widely used in aerospace, abrasives, semiconductors, and other fields because of its high strength, hardness, resistivity, and many other excellent properties. Alumina has a delicate surface and hard texture, with a Mohs hardness of about 9, second only to diamond. It can effectively remove protruding parts of the surface of hard materials to achieve a higher material removal rate; it is chemically relatively stable and is not easy to react with most chemicals, so it can maintain polishing during the CMP process.
The life of the liquid: compared with other advanced abrasives, the cost of alumina is relatively low, so it has more advantages in industrial applications. However, because the surface of alumina abrasives is prone to positive or negative charges, resulting in electrostatic gravity, Van der Waals force, and other inter-molecular forces, it is easier to agglomeration in the polishing solution, and its own hardness is high. If the CMP process is not operated properly, it can easily lead to an uneven material removal rate. Mechanical damage is caused on the material’s surface, so caution is required when using it.

Alumina SEM diagram
Cerium Oxide CeO2
Cerium oxide is an abrasive with excellent polishing properties. It has strong cutting force, short polishing time, long service life, and high accuracy. It is often used in polishing optical glass devices, TV picture tubes, semiconductor wafers and other devices. Cerium oxide has good chemical stability in the polishing process and cannot easily react adversely with other components in the polishing solution. It is conducive to maintaining the stability and service life of the polishing solution. Compared with other abrasives, it has less environmental impact and meets the current requirements of green chemistry and sustainable development. The Mohs hardness of cerium oxide is about 7, similar to the hardness of glass. It has excellent polishing properties for SiO2-quality materials. It can have a higher cutting rate while considering the surface quality.
*Principle of action: Under pressure, the water molecules in the polishing solution will hydroxylate the surface of the SiO2 wafer, and CeO2 will form a Ce-O-Si bond with SiO2. Due to the easy hydrolysis of the glass surface, the Ce-O-Si (OH) 3 bond is formed. The bond between CeO2 and the polishing platform, Mechanical force urges the Si-O-Si bond to break, and SiO2 will be thrown away by CeO2 in a blocky form. In this process, the Ce-O-Si bond formation is the reaction’s control step. Its formation increases the polishing shear stress, and the entire polishing speed is affected by the Ce-O-Si bond. The breaking speed of the Si-O-Si bond affects the formation.
In addition, cerium oxide is also a semiconductor photocatalyst. It has a variable valence state (Ce4+, Ce3+) and rich oxygen vacancies. It combines tribochemical ability and photochemical oxidation activity and can be applied to photocatalytic-assisted polishing.
Out of the above common abrasive particles, other abrasives, such as iron oxide and silicon carbide, may also be used in CMP polishing. These abrasives may have advantages in certain applications or polishing of specific materials. In practical applications, the influence of factors such as particle size and concentration of abrasive particles on the polishing effect needs to be considered. By reasonably selecting and using abrasive particles, an efficient and high-precision CMP polishing process can be realized to meet the needs of various precision machining applications.