Aerospace manufacturing stands at the forefront of high-tech industries, embodying advanced manufacturing techniques that push the boundaries of material science and engineering. The development of cutting-edge aircraft engines, such as the F119 from Pratt & Whitney, the F120 from General Electric, and the M88-2 from SNECMA, exemplifies this trend. These engines are characterized by their use of new materials, innovative processes, and advanced technologies that collectively represent the pinnacle of global aerospace engineering.
Understanding Ultra-High Strength Steel
What is Ultra-High Strength Steel?
Ultra-high strength steel (UHSS) emerged in the mid-20th century, with significant advancements occurring in the 1940s and 1950s when materials like Cr-Mo steel (AISI 4130) and Cr-Ni-Mo steel (AISI 4340) were developed. These steels exhibited tensile strengths of 170 kgf/mm² and 190 kgf/mm², respectively. Further enhancements led to the creation of 300M steel, which boasts a tensile strength of 190-210 kgf/mm². The evolution continued into the 1960s with the introduction of martensitic aging steel, achieving a tensile strength of approximately 180 kgf/mm².
The requirements for UHSS are stringent: they must possess not only high tensile strength but also sufficient toughness, a high strength-to-weight ratio, and excellent weldability. This necessitates advanced metallurgical processes such as electric arc furnace melting and vacuum induction melting to ensure purity. For instance, the landing gear of second-generation aircraft utilized 30CrMnSiNi2A steel with a tensile strength of 1700 MPa, while third-generation fighters demand materials capable of withstanding over 5000 flight hours.

High-Temperature Alloy Materials
What are High-Temperature Alloys?
High-temperature Alloys are categorized based on their operational temperature ranges: materials that endure temperatures up to 760°C, 1200°C, and even 1500°C. These alloys are crucial for components in gas turbine engines due to their exceptional high-temperature strength and resistance to oxidation and thermal corrosion.
The development of these materials began in the late 1930s, with significant advancements during World War II to meet the demands of new aircraft engines. Notable innovations include nickel-based alloys like Inconel for jet engine combustion chambers and cobalt-based alloys that have been used in various high-temperature applications.
Metal Intermetallic Compounds
What are Metal Intermetallic Compounds?
Metal intermetallic compounds form when metals combine with non-metals or other metals in specific ratios, resulting in unique crystalline structures. These compounds exhibit remarkable properties such as high-temperature stability and superior strength-to-weight ratios, making them ideal for aerospace applications.
Research has focused on titanium-aluminum (TiAl) and nickel-aluminum (NiAl) intermetallics due to their lightweight nature and high operational temperatures. For example, TiAl can function effectively at temperatures up to 982°C, making it suitable for turbine components in advanced aircraft engines.
Metal Matrix Composites
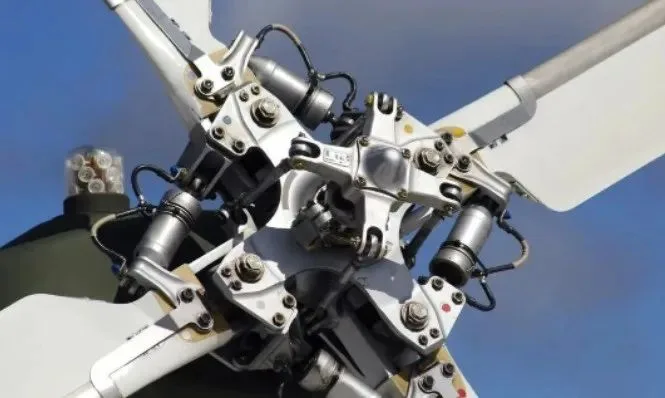
What are Metal Matrix Composites?
Metal matrix composites (MMCs) consist of metal or alloy matrices reinforced with other materials such as ceramics or carbon fibers. They provide enhanced mechanical properties while maintaining lightweight characteristics essential for aerospace applications.
MMCs offer improved tensile strength, thermal conductivity, and resistance to wear compared to traditional materials. For instance, carbon fiber-reinforced aluminum composites are utilized in manufacturing turbine fan blades due to their excellent performance under stress.
A Sum Up – Specific Materials Used in Advanced Aircraft Engine
1. High-Temperature Alloys
High-temperature alloys, particularly Nickel, Cobalt, and Iron-based superalloys, are essential for components that operate under extreme conditions. These materials exhibit exceptional high-temperature strength, oxidation resistance, and fatigue performance. They are primarily used in turbine blades, turbine disks, and combustion chambers of jet engines. For instance, the F119 engine from Pratt & Whitney incorporates high-temperature alloys that withstand temperatures exceeding 1,000°C while maintaining structural integrity.

2. Titanium Alloys
Titanium Alloys are known for their high strength-to-weight ratio and corrosion resistance. They are extensively used in airframes and engine components where weight savings are crucial. The development of titanium-aluminum alloys has further improved performance in high-pressure environments. For example, titanium alloys are utilized in the hydrogen pump impellers of the Long March 5B rocket engines, showcasing their capability in demanding aerospace applications.
3. Metal Intermetallic Compounds
Metal intermetallic compounds, such as titanium-aluminum (TiAl) and nickel-aluminum (NiAl), have gained attention for their lightweight properties and high-temperature stability. These compounds can operate at temperatures up to 982°C and provide excellent oxidation resistance and creep strength. Their application in advanced engines like the F120 has demonstrated significant improvements in efficiency and weight reduction.
4. Ceramic Matrix Composites (CMCs)
CMCs are increasingly being adopted due to their exceptional thermal stability and lightweight characteristics. These composites can withstand temperatures beyond 1400°C and offer superior resistance to thermal shock compared to traditional metal materials. The use of silicon carbide fiber-reinforced CMCs is becoming common in turbine components, enhancing overall engine performance.
5. Carbon-Carbon Composites
Carbon-carbon composites are utilized in specific high-temperature applications within jet engines due to their lightweight nature and ability to withstand extreme temperatures. Recent advancements have improved their oxidation resistance, making them suitable for components such as afterburner nozzles and combustion chambers in engines like the F119.
6. Ultra-High Strength Steel
Ultra-high strength steel is critical for structural components that require both strength and toughness. This material is often used in landing gear systems due to its ability to handle significant loads while minimizing weight. The development of advanced heat treatment processes has enhanced the performance characteristics of these steels.
7. Resin Matrix Composites
While primarily used in non-metallic applications, resin matrix composites are being integrated into aerospace designs for various components due to their lightweight properties and ease of manufacturing. These materials provide good mechanical properties while reducing overall weight, contributing to fuel efficiency.
Conclusion
The ongoing advancements in materials science within aerospace manufacturing not only enhance the performance and longevity of aircraft components but also drive innovation across various sectors. The integration of ultra-high strength steels, high-temperature alloys, metal intermetallic compounds, and metal matrix composites ensures that modern aircraft meet increasingly stringent performance criteria while remaining lightweight and durable. As these technologies continue to evolve, they will undoubtedly play a pivotal role in shaping the future of aerospace engineering.
Related Product – Refractory Metals
- Molybdenum(Mo)
- Tantalum(Ta)
- Tungsten(W)
- Titanium(Ti)
- Niobium(Nb)
- Zirconium(Zr)
- Vanadium(V)
- Rhenium(Re)
- Rhodium(Rh)
- Iridium(Ir)
- Chromium(Cr)
Related Product – Alloys
- Tungsten Rhenium Alloy
- Tantalum Tungsten Alloy
- Tungsten Heavy Alloy
- Other Tungsten Alloys
- TZM Alloy
- Molybdenum Rhenium Alloy
- Molybdenum Tungsten Alloy
- Molybdenum Lanthanum Alloy
- Other Molybdenum Alloys