Welcome to the fascinating world of titanium nickel alloys! In this article, we will take a deep dive into the secrets of Nitinol, Inconel, and Austenite Shape Memory Alloy. These incredible alloys have captured the attention of scientists, engineers, and even the medical community due to their unique properties and applications.
Nitinol, known for its remarkable shape memory and superelasticity, has revolutionized the field of biomedical engineering. From stents that adapt to the body’s temperature and shape to orthodontic wires that deliver constant pressure, Nitinol is at the forefront of cutting-edge medical devices.
Meanwhile, Inconel, a high-performance alloy known for its outstanding resistance to heat and corrosion, finds applications in industries such as aerospace, automotive, and chemical processing. Its strength, durability, and ability to withstand extreme temperatures make it an invaluable material for applications that demand reliability under harsh conditions.
And then there’s austenite shape memory alloy, which showcases a unique shape memory effect. With applications ranging from robotics and smart materials to actuators and sensors, it’s no wonder that this alloy is capturing the attention of researchers across various fields.
Join us as we unravel the secrets and possibilities of these incredible titanium nickel alloys. Get ready to be amazed by the remarkable characteristics and potential applications of Nitinol, Inconel, and austenite shape memory alloy.
Understanding Nitinol and its properties
Nitinol, a titanium nickel alloy, is a remarkable material that has captured the attention of scientists, engineers, and medical professionals worldwide. This alloy is renowned for its unique properties, including shape memory and superelasticity, which have revolutionized various industries.
At the heart of Nitinol’s remarkable characteristics lies its unique atomic structure. The alloy is composed of nearly equal parts of titanium and nickel, which form a crystal structure that can undergo a phase transformation when subjected to changes in temperature or stress. This phase transformation is the key to Nitinol’s shape memory and superelastic behavior, making it a highly versatile and sought-after material.
The shape memory effect of Nitinol is particularly fascinating. When the alloy is deformed, it can “remember” its original shape and return to it when heated or unloaded. This property allows Nitinol to be bent, twisted, or compressed, and then regain its original form when the external force is removed. This remarkable ability has found numerous applications in the medical field, where Nitinol’s shape memory is used to create stents, orthodontic wires, and other implantable devices that can adapt to the body’s unique contours and requirements.
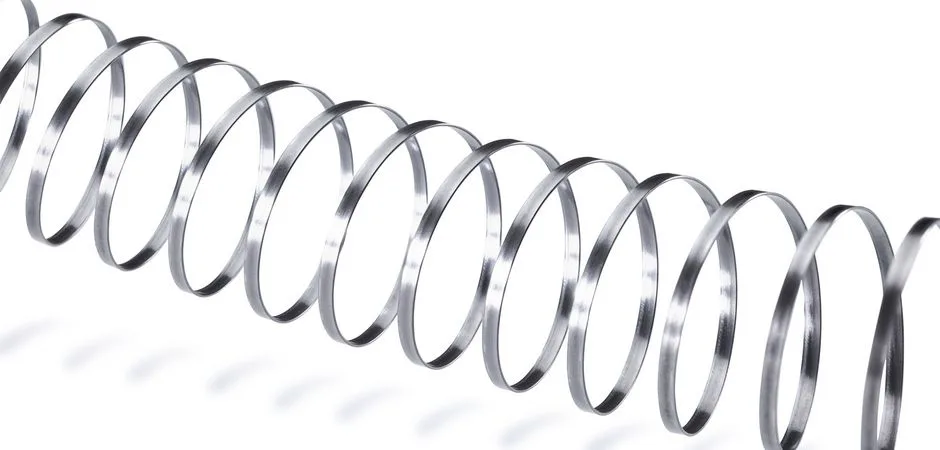
Exploring the characteristics of Inconel
Inconel, another titanium nickel alloy, is renowned for its exceptional resistance to heat and corrosion, making it a highly sought-after material in various industries. This alloy’s unique composition and manufacturing process give it a distinct set of properties that set it apart from other metals and alloys.
One of the standout characteristics of Inconel is its ability to maintain its strength and integrity even at extremely high temperatures. This heat resistance is a result of the alloy’s stable austenitic microstructure, which is resistant to oxidation and scaling. This makes Inconel an ideal choice for applications in the aerospace, automotive, and chemical processing industries, where components are subjected to intense heat and harsh environments.
In addition to its heat resistance, Inconel also boasts excellent corrosion resistance. The alloy’s composition, which includes chromium and nickel, forms a protective oxide layer that shields the underlying material from the damaging effects of various corrosive agents, such as acids, salts, and harsh chemicals. This property makes Inconel a popular choice for equipment and components used in the petrochemical, marine, and power generation industries, where corrosion is a constant challenge.
The fascinating properties of austenite shape memory alloy
Austenite shape memory alloy, a subclass of titanium nickel alloys, is known for its unique shape memory effect, which sets it apart from other metallic materials. This alloy’s ability to “remember” and recover its original shape after undergoing deformation has captured the attention of researchers and engineers across various fields.
The shape memory effect in austenite shape memory alloy is a result of its phase transformation behavior. At lower temperatures, the alloy exists in a martensitic phase, which is relatively soft and easily deformable. When the alloy is heated, it undergoes a phase transformation to the austenitic phase, which is harder and more rigid. This phase transformation is reversible, allowing the alloy to “remember” its original shape and return to it when heated.
The shape memory effect in austenite shape memory alloy is not limited to temperature-induced changes. The alloy can also exhibit a superelastic behavior, where it can undergo significant deformation and then recover its original shape without the application of heat. This superelasticity is a result of the stress-induced phase transformation from austenite to martensite, which occurs when the alloy is subjected to mechanical stress.
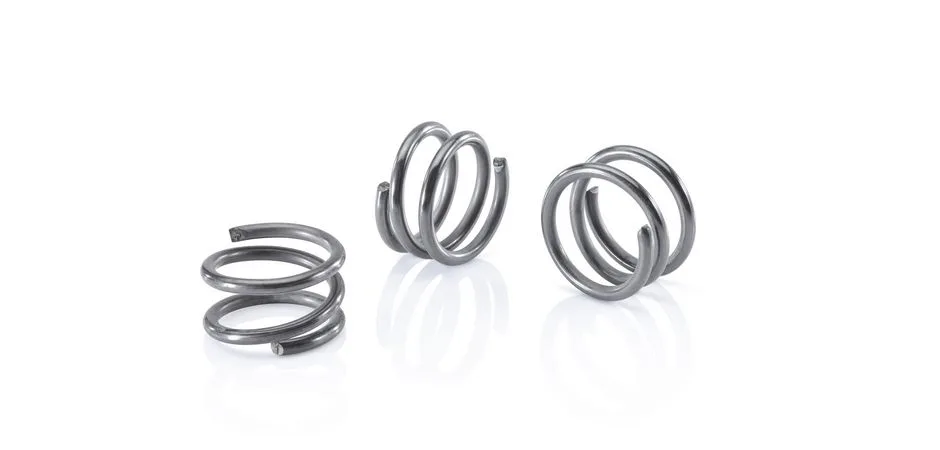
Applications and uses of titanium nickel alloys
The unique properties of titanium nickel alloys, including Nitinol, Inconel, and austenite shape memory alloy, have led to a wide range of applications across various industries. These alloys have revolutionized fields such as biomedical engineering, aerospace, and robotics, among others.
In the biomedical field, Nitinol has been a game-changer. Its shape memory and superelastic properties have enabled the creation of innovative medical devices, such as stents, orthodontic wires, and surgical tools. Nitinol stents, for example, can be compressed for easy insertion into the body and then expand to their original shape, conforming to the patient’s unique anatomy and providing effective support for blood vessels or other structures. Nitinol orthodontic wires, on the other hand, can deliver a constant, gentle force to the teeth, leading to more efficient and comfortable treatment.
Beyond the medical realm, titanium nickel alloys have found applications in the aerospace industry. Inconel, with its exceptional heat and corrosion resistance, is widely used in the manufacture of aircraft engines, turbines, and other high-temperature components. Its ability to maintain its strength and integrity under extreme conditions makes it an essential material for ensuring the safety and reliability of these critical systems.
In the field of robotics and smart materials, austenite shape memory alloy has shown great potential. Its unique shape memory effect and superelasticity have enabled the development of actuators, sensors, and other intelligent systems that can respond to changes in temperature or mechanical stress. These applications have the potential to revolutionize the way we interact with and control various devices and systems.
Manufacturing process of titanium nickel alloys
The production of titanium nickel alloys, such as Nitinol, Inconel, and austenite shape memory alloy, involves a complex and precisely controlled manufacturing process. This process is crucial in ensuring the consistent and reliable performance of these alloys, as their unique properties are heavily dependent on the composition and microstructure of the material.
The manufacturing of titanium nickel alloys typically begins with the melting and alloying of the raw materials, which include titanium and nickel, as well as other alloying elements depending on the specific alloy being produced. This melting process is often carried out in a vacuum or inert atmosphere to prevent the introduction of impurities that could compromise the alloy’s properties.
Once the molten alloy is obtained, it undergoes a series of processing steps, such as casting, rolling, or forging, to shape the material into the desired form. The specific processing methods used will depend on the intended application of the alloy and the required mechanical properties. For example, Nitinol components for medical devices may be produced using a combination of casting, cold working, and heat treatment to achieve the desired shape memory and superelastic behavior.
Throughout the manufacturing process, strict quality control measures are implemented to ensure the consistent composition and microstructure of the titanium nickel alloy. This includes careful monitoring of temperature, pressure, and other critical parameters during each processing step. Additionally, extensive testing and characterization are conducted to verify the alloy’s performance and compliance with industry standards and regulations.
Advantages and disadvantages of titanium nickel alloys
Titanium nickel alloys, such as Nitinol, Inconel, and austenite shape memory alloy, offer a unique set of advantages that have made them highly sought-after materials in various industries. However, like any material, they also have some inherent disadvantages that must be considered when selecting the appropriate alloy for a specific application.
One of the primary advantages of titanium nickel alloys is their exceptional strength-to-weight ratio. These alloys are known for their high strength and durability, yet they are relatively lightweight compared to other metallic materials. This makes them ideal for applications where weight is a critical factor, such as in the aerospace and automotive industries.
Another significant advantage of titanium nickel alloys is their remarkable corrosion resistance. The presence of chromium and nickel in the alloy composition creates a protective oxide layer that shields the underlying material from the damaging effects of various corrosive agents. This property is particularly valuable in industries where components are exposed to harsh environments, such as the chemical processing, marine, and power generation sectors.
However, one of the potential disadvantages of titanium nickel alloys is their relatively high cost compared to other metallic materials. The production process, which involves precise control of composition and microstructure, can be complex and resource-intensive, leading to higher manufacturing costs. This can be a barrier to widespread adoption, particularly in applications where cost is a significant factor.
Additionally, the unique properties of titanium nickel alloys, such as shape memory and superelasticity, can also present challenges in terms of manufacturing and processing. Achieving the desired properties often requires specialized techniques and equipment, which can add to the overall cost and complexity of the manufacturing process.
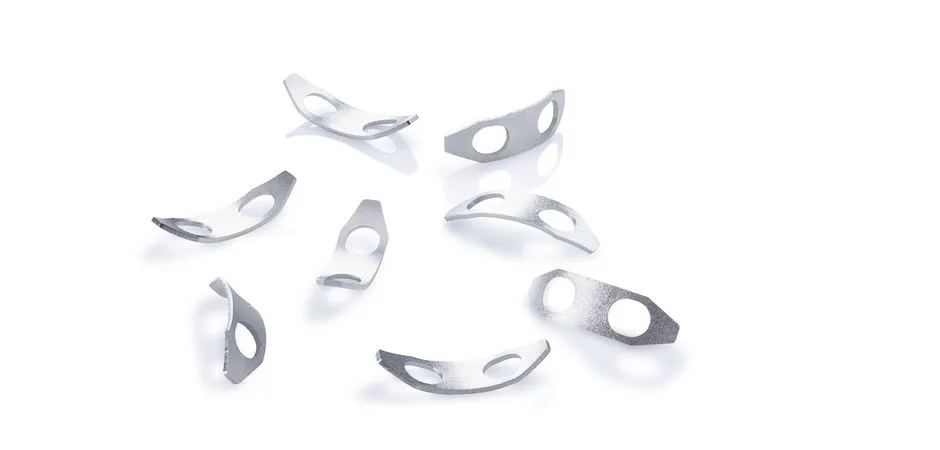
Innovations and developments in the field of titanium nickel alloys
The field of titanium nickel alloys is constantly evolving, with researchers and engineers continuously exploring new ways to harness the unique properties of these materials. From advancements in manufacturing techniques to the development of novel applications, the world of titanium nickel alloys is brimming with exciting innovations and breakthroughs.
One area of active research and development is the optimization of the manufacturing process for titanium nickel alloys. Scientists are exploring new methods, such as additive manufacturing and advanced casting techniques, to improve the consistency and performance of these materials. By fine-tuning the composition, microstructure, and processing parameters, researchers aim to unlock even greater potential in Nitinol, Inconel, and austenite shape memory alloy.
Another exciting frontier in the field of titanium nickel alloys is the exploration of new applications. As the understanding of these materials deepens, engineers are finding innovative ways to leverage their shape memory, superelasticity, and heat resistance in diverse industries. For instance, the use of Nitinol in medical devices continues to expand, with researchers exploring its potential in areas such as tissue engineering, drug delivery, and minimally invasive surgical procedures.
In the field of smart materials and robotics, the shape memory effect of austenite shape memory alloy has opened up new possibilities. Researchers are developing advanced actuators, sensors, and adaptive structures that can respond to changes in temperature or mechanical stress, paving the way for the creation of more intelligent and responsive systems. These innovations have the potential to revolutionize fields like aerospace, automotive, and even consumer electronics.
As the demand for high-performance, durable, and versatile materials continues to grow, the importance of titanium nickel alloys will only increase. With ongoing advancements in manufacturing, processing, and application development, the future of these remarkable alloys is truly exciting, promising even more remarkable discoveries and breakthroughs in the years to come.
Comparison of Nitinol, Inconel, and austenite shape memory alloy
Nitinol, Inconel, and austenite shape memory alloy are all titanium nickel alloys, but they each possess unique characteristics and properties that make them suitable for different applications. Understanding the similarities and differences between these alloys is crucial in selecting the right material for a given task.
Nitinol is primarily known for its exceptional shape memory and superelasticity. These properties make it a popular choice in the biomedical field, where its ability to adapt to the body’s shape and temperature is highly valuable for applications such as stents, orthodontic wires, and surgical tools. Nitinol’s unique behavior is a result of its phase transformation between the austenitic and martensitic phases.
In contrast, Inconel is renowned for its outstanding resistance to heat and corrosion. This high-performance alloy is widely used in the aerospace, automotive, and chemical processing industries, where components are subjected to extreme temperatures and harsh environments. Inconel’s stable austenitic microstructure and protective oxide layer are the key factors behind its exceptional durability and reliability.
Austenite shape memory alloy, on the other hand, showcases a distinct shape memory effect that is driven by a reversible phase transformation between the austenitic and martensitic phases. This property has led to the development of innovative applications in the field of robotics, smart materials, and actuators. Austenite shape memory alloy’s ability to “remember” and recover its original shape after deformation has captured the attention of researchers and engineers across various industries.
While Nitinol, Inconel, and austenite shape memory alloy share a common titanium nickel base, their unique compositions and manufacturing processes result in distinct properties and applications. Understanding these differences is crucial when selecting the appropriate alloy for a specific project or industry, ensuring the best possible performance and reliability.
Conclusion
In the captivating world of titanium nickel alloys, Nitinol, Inconel, and austenite shape memory alloy have each carved out their own remarkable niches, showcasing their unparalleled capabilities and potential. From the shape memory and superelasticity of Nitinol to the heat and corrosion resistance of Inconel, and the fascinating shape memory effect of austenite shape memory alloy, these alloys have transformed industries and captured the imagination of scientists, engineers, and medical professionals alike.
As we delve deeper into the secrets of these remarkable materials, the possibilities seem endless. The ongoing innovations and developments in manufacturing processes, application design, and material optimization promise even more remarkable discoveries and breakthroughs in the years to come.
Whether it’s the life-saving medical devices powered by Nitinol, the reliable and durable components found in aerospace and industrial applications, or the intelligent systems enabled by austenite shape memory alloy, these titanium nickel alloys continue to push the boundaries of what’s possible. As we explore this fascinating world, we can’t help but be amazed by the incredible potential of these materials and the transformative impact they have had, and will continue to have, on our world.
Related Product
- Tungsten Rhenium Alloy
- Tantalum Tungsten Alloy
- Tungsten Heavy Alloy
- Other Tungsten Alloys
- TZM Alloy
- Molybdenum Rhenium Alloy
- Molybdenum Tungsten Alloy
- Molybdenum Lanthanum Alloy
- Other Molybdenum Alloys